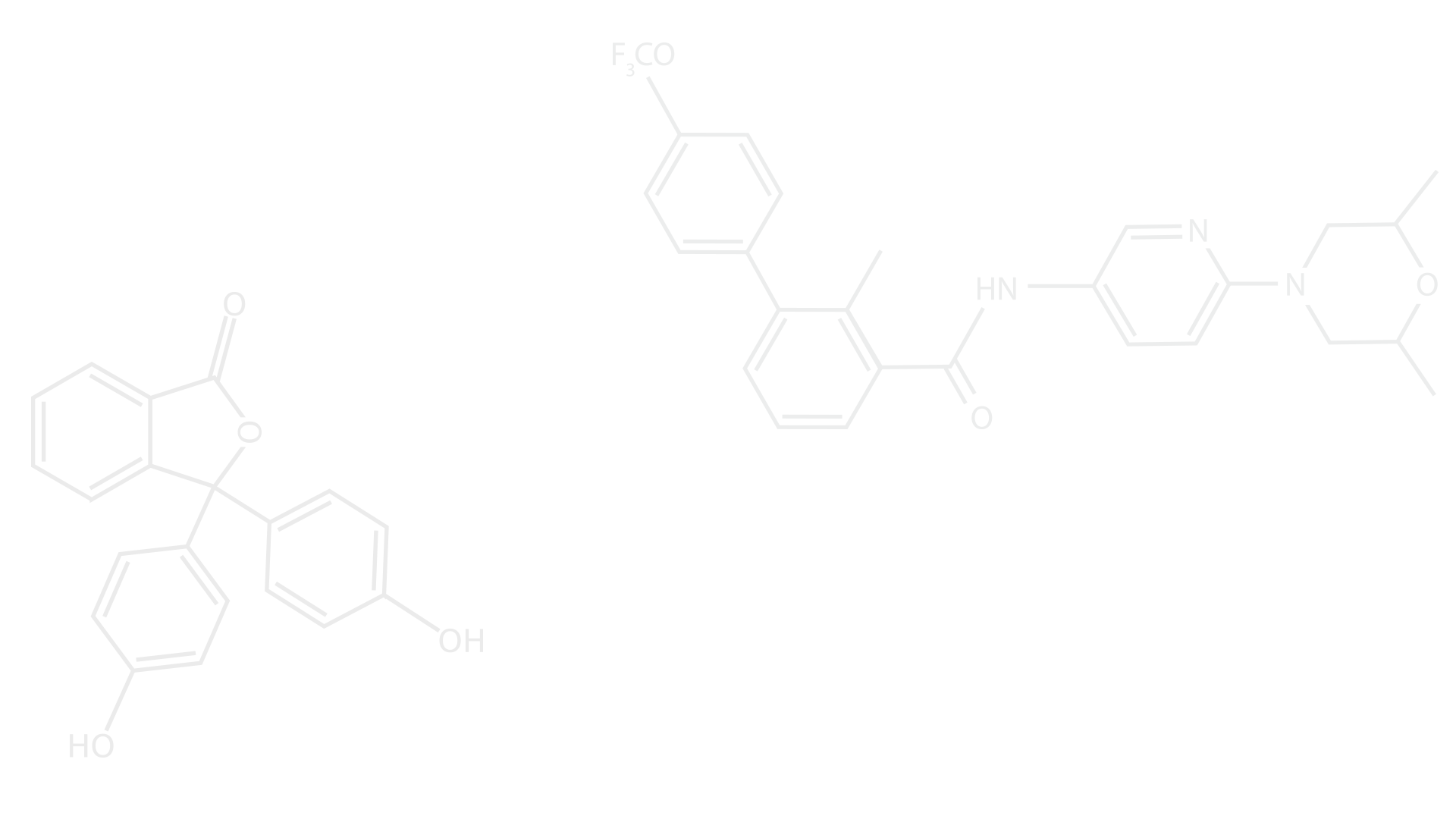

Work Experience
(2020-Ongoing)
Graduate Teaching and Research Assistant
Florida Atlantic University, United States
(2016 - 2020)
Senior Process Research Engineer
Engro Fertilizers Limited, Pakistan
(2014 - 2016 )
Process Research Engineer
Engro Fertilizers Limited, Pakistan
​
(July 2013)
Internee, Process Engineering Department
Sitara Chemicals Limited, Pakistan.
​
Graduate Research/Teaching Assistant
​
-
Assisted instructors with conducting virtual and in-person labs for Introduction to Environmental Engineering (ENV3001C) and Fundamentals of Engineering (EGN1002)
-
Facilitated professors with exam and homework grading and helped students with the problem during office hours
​
Senior Process Research Engineer- Ammonia & Urea Plant
​
-
Devising a fiscal approach for farmers by improvement in Nitrogen Use Efficiency (NUE) of Urea Prills-Azadirachta Indica (Neem) coating on urea.
-
Approaching performance of CSTR in a PFR- Study on modernization of Urea Reactor by replacement of sieve trays with High Efficiency SuperCup trays (HET).
-
Automating Ammonia and Urea plants—study on Installation of Advanced Process Control at Ammonia/Urea Complex
-
Modeling urea plant’s MP loop using Aspen Plus and up-gradation of MP condenser to reduce ammonia loss from plant.
-
Recovering continuous waste of Urea as a fuel in Furnace -Technical evaluation and feasibility analysis of recovering Urea plant MP loop vent gases in Primary Reformer (furnace) as a fuel.
​
Process Research Engineer- Ammonia Plant
​
-
Preventing the plant downtime and production loss- Replacing Hydrogen Recovery Unit membrane online by double block and bleed arrangement provision at ammonia plant.
-
Flooded High Temperature Shift Converter catalyst; Loss of millions saved- Improbable successful dry-out after water ingress due to Boiler Feed Water Pre-heater failure.
-
Hydraulic analysis of cooling water circuits and root cause analysis of limiting cooling water exchanger in Backend of Ammonia plant.
-
Issuance of Technical Monitoring Program (TMP) and Catalyst evaluation reports on biannual basis and subsequent removal of efficiency related bottlenecks.
-
Comparison and feasibility analysis for various catalysts/technologies with respect to plant requirements and rate of return.
-
Financial Savings by increasing Ammonia backend pressure above design via building up inerts in loop.
​​
Intern, Process Engineering department
​
-
Modeling and dynamic simulations of Caustic Soda unit (32% and 50% Purity) using Aspen Hysys.
-
Performance comparison of design material balance with current operating conditions.
standards for designing of different instrument, equipment and machines
Certifications​
-
ASQ CSSBB
-
ASQ CSSGB